Automotive
The automotive sector is constantly evolving in search of faster and more profitable production, towards a more sustainable, efficient future. Hot Isostatic Pressing (HIP) technology accompanies the production processes in this sector and is in line with the needs of the automotive industry.
By ensuring lighter weight, superior performance and greater durability, HIP technology solutions can be used on a variety of parts, from small components to larger parts with more complex shapes.
Combining profitability and innovation, HIP is one of the best tools to optimize manufacturing processes, particularly in the field of prototyping.
Automotive HIP applications: parts, materials, techniques
The automotive industry is an engine of innovation in the field of materials and its uses for HIP technology are growing every day.
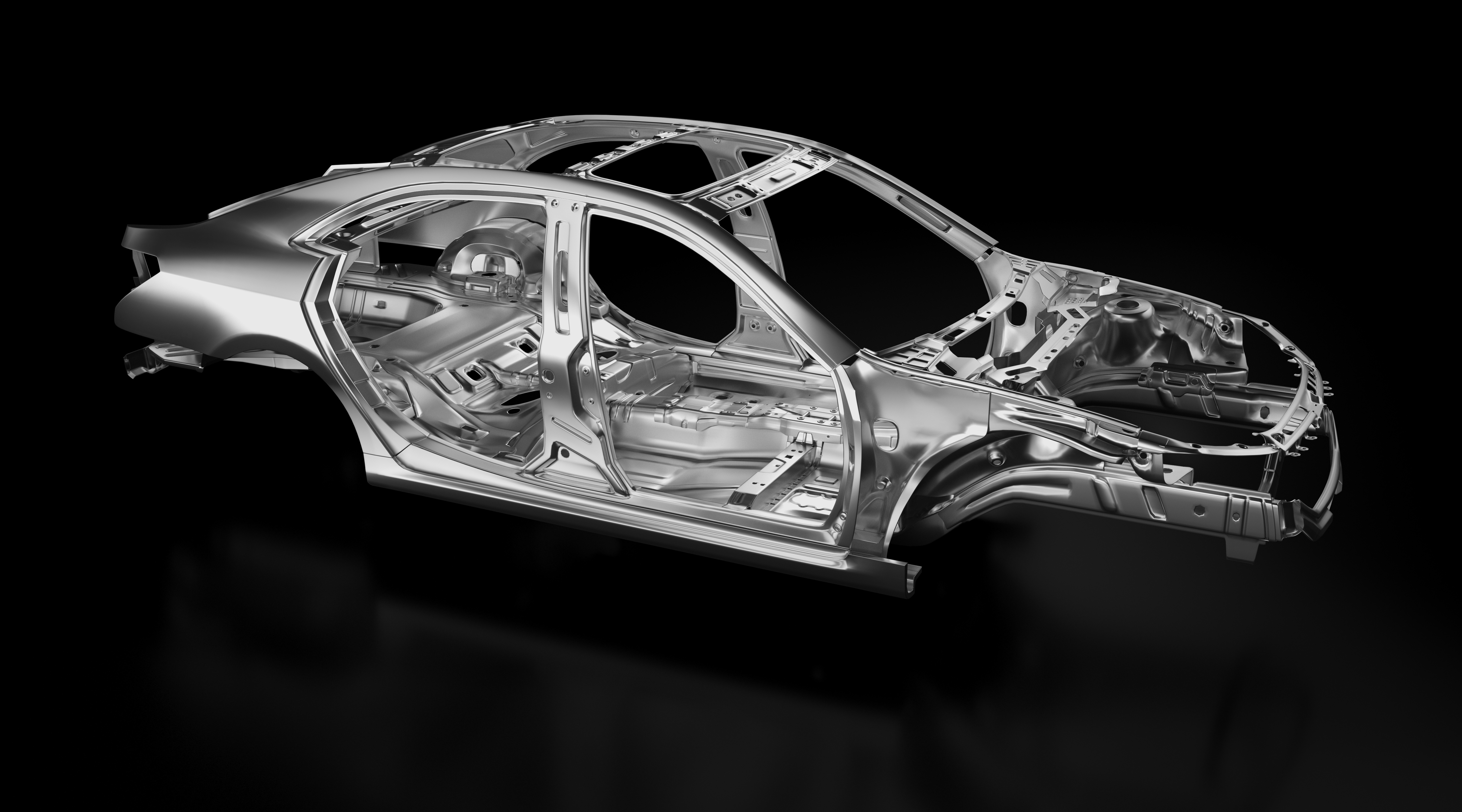

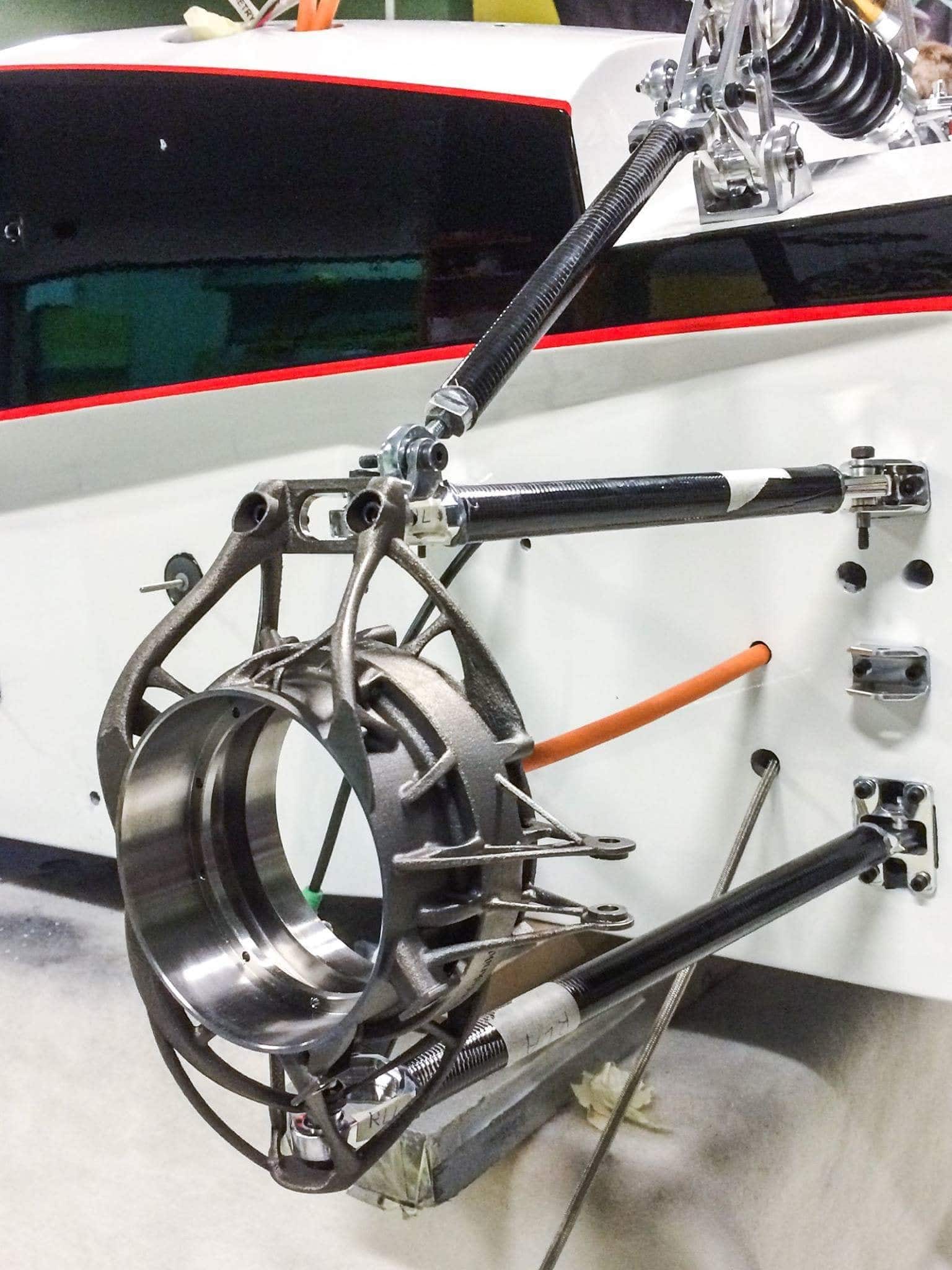
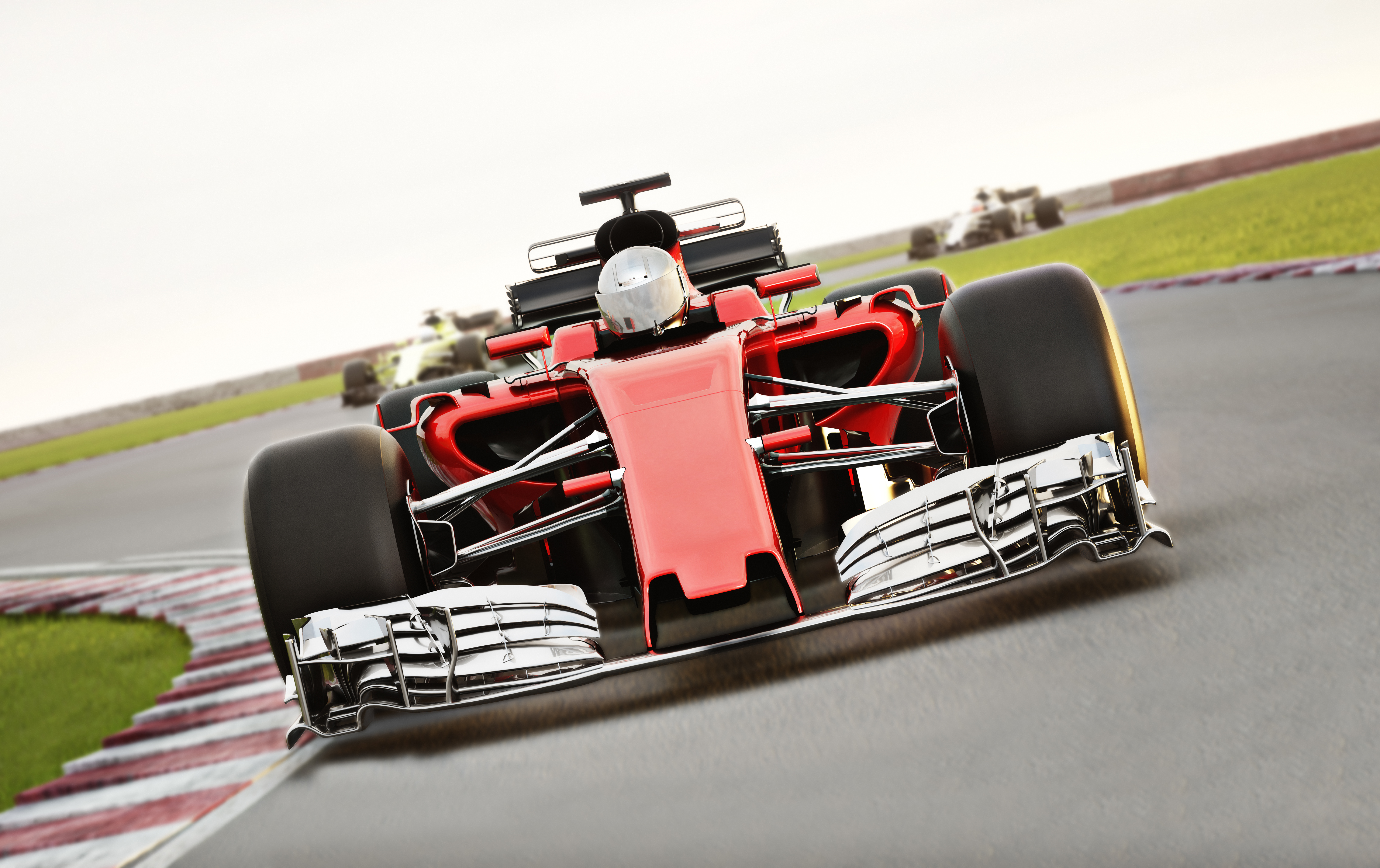
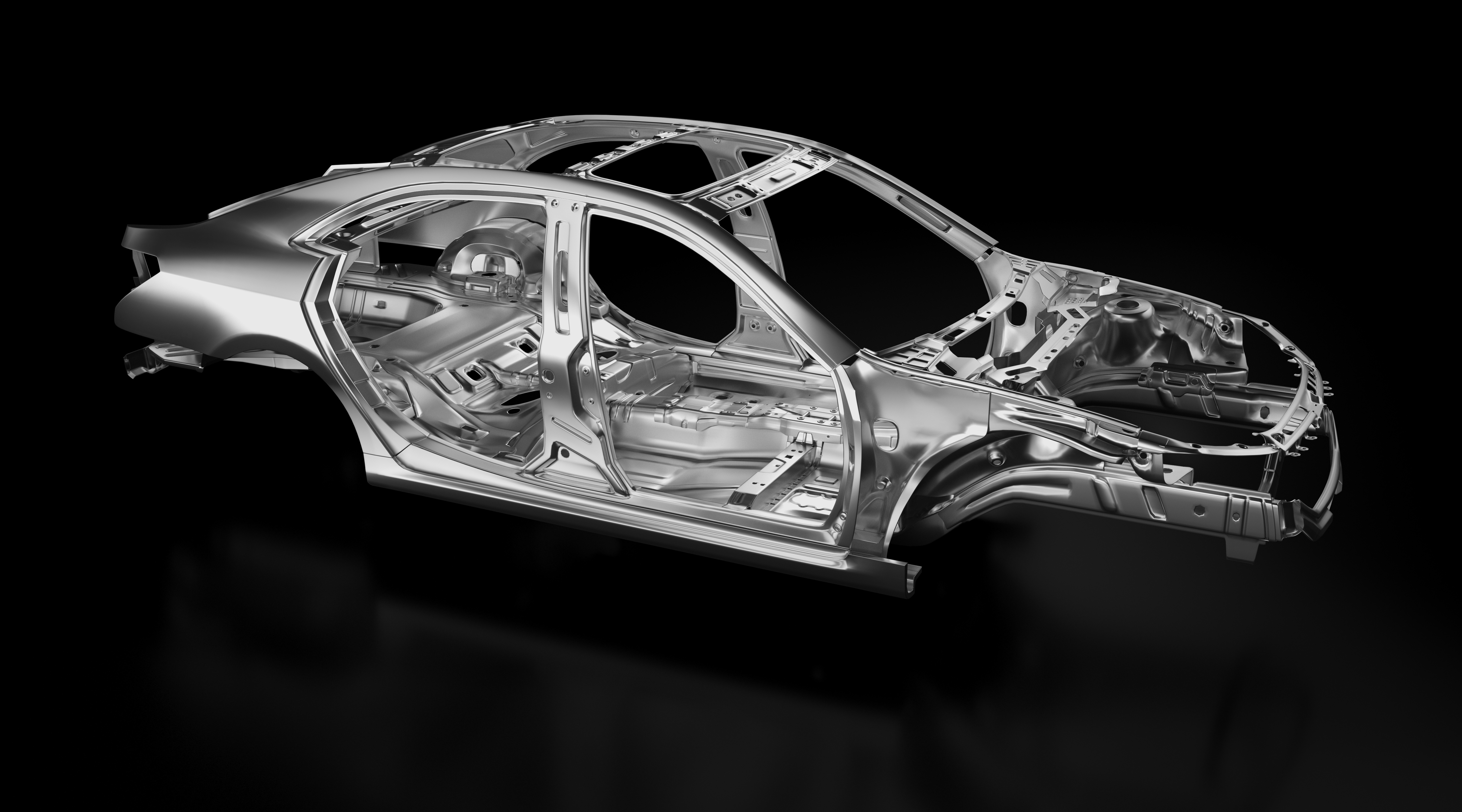

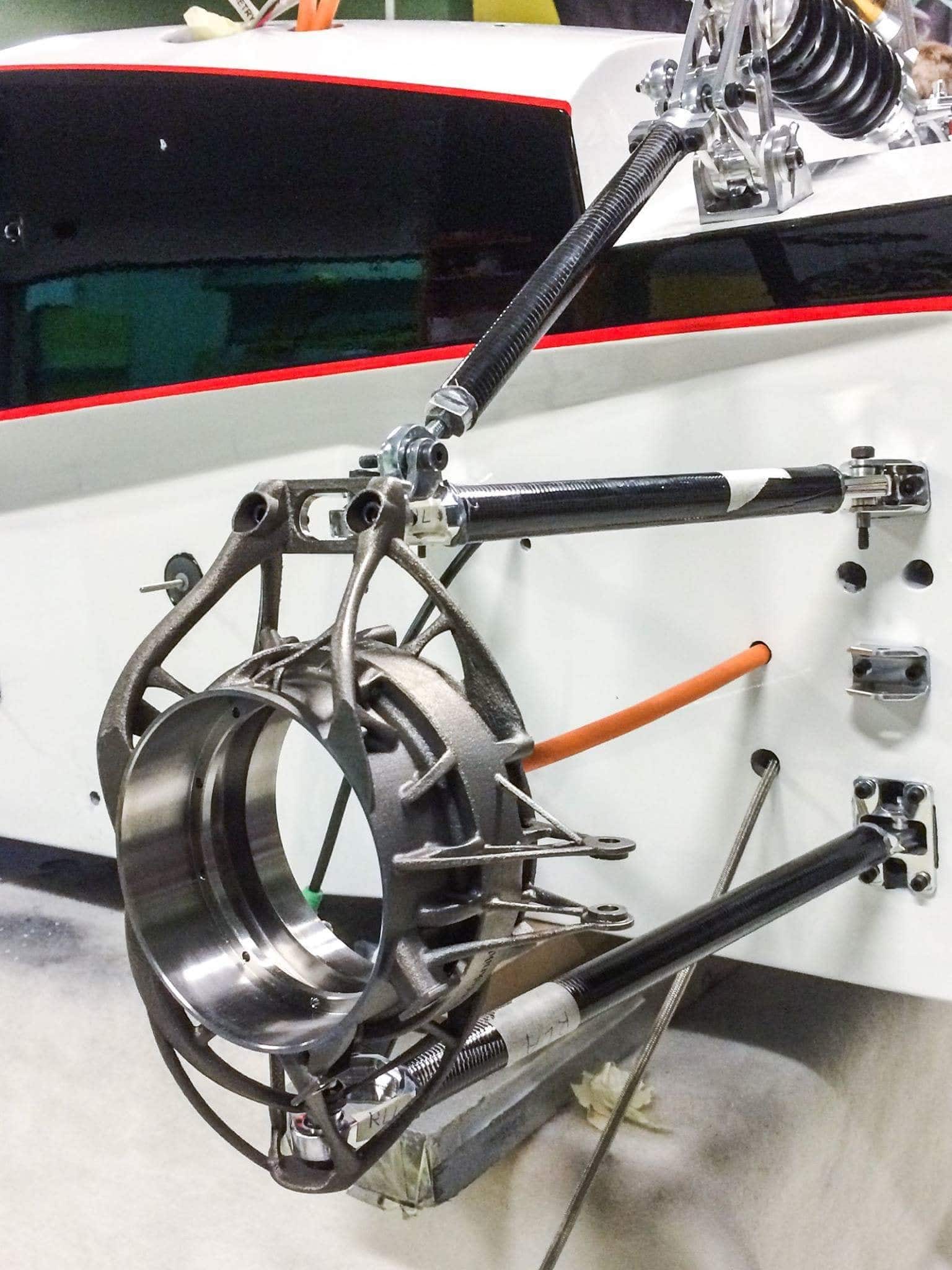
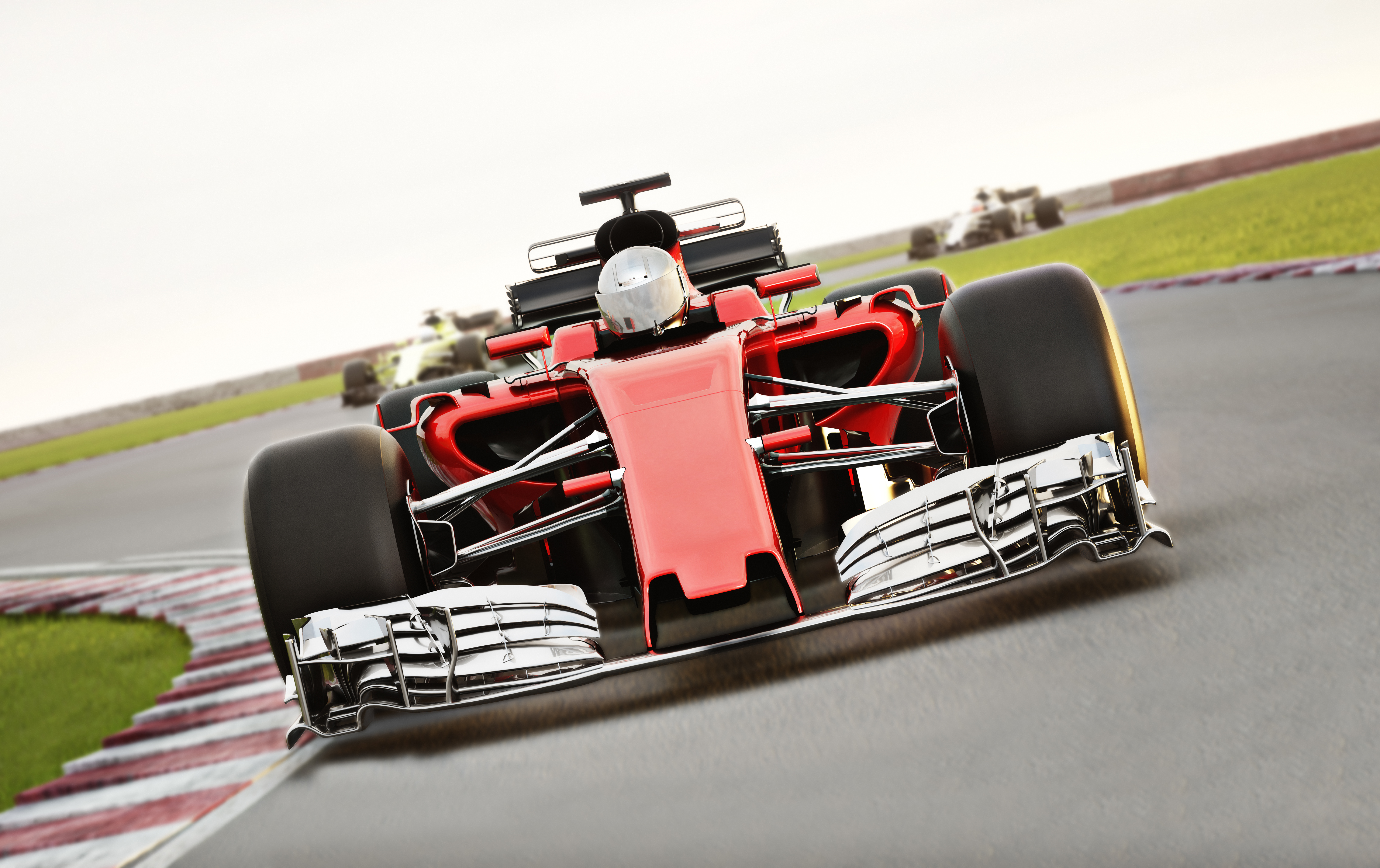
MAIN BENEFITS OF USING HIP IN THE AUTOMOTIVE SECTOR
For the automotive sector, the use of Hiperbaric's HIP technology provides multiple benefits, such as the following:
Improves material properties and performance
- Increases the mechanical properties of the parts.
- Improves fatigue life in high performance materials.
Reaches 100% of the theoretical density of the parts
- Densifies porosities and eliminates possible internal defects, provided by certain techniques such as Additive Manufacturing (AM).
- Gives greater statistical consistency to high performance materials.
Certificates
The quality standard in the automotive industry is the CQI-9, which focuses on continuous improvement in the heat treatment processes carried out. This standard was published by the American Automobile Association (AIAG - Automotive Industry Action Group). This is not a standard in itself, but a self-evaluation that must be carried out at least once a year in order to prevent defects and reduce waste in the supply chain.