Medical Implants
The world market for medical implants has experienced significant growth over the past decades and is expected to continue to increase in the coming years. According to the WHO, between 2015 and 2050, the proportion of the world's population over 60 will increase from 900 million to 2 billion, an increase from 12% to 22%. This rapid aging of the world's population, together with the increasing prevalence of chronic diseases, will lead to a significant increase in the demand for medical implants.
In addition, this market is going to experience an important revolution thanks to the possibilities of customization made possible by new technologies such as Additive Manufacturing. The implants will adapt perfectly to each patient's anatomy, increasing the success of surgery and reducing the need for rehabilitation.
The medical implant sector will be able to fully benefit from the design freedom offered by Additive Manufacturing (AM) thanks to Hot Isostatic Pressing (HIP), which makes it possible to optimize the properties of the materials by eliminating porosity and internal defects.
HIP applications in medical implants: parts, materials, techniques
Bones and joints suffer significant stresses every time we make movements. When these fail, they are usually replaced by metal implants that must be sufficiently resistant and durable. These implants are usually manufactured from chrome cobalt alloys (Co-Cr) or Titanium using technologies such as powder metallurgy (PM), metal injection molding (MIM) or additive manufacturing (AM). Since these are elements that will be subject to cyclical stresses, their fatigue behavior is critical.
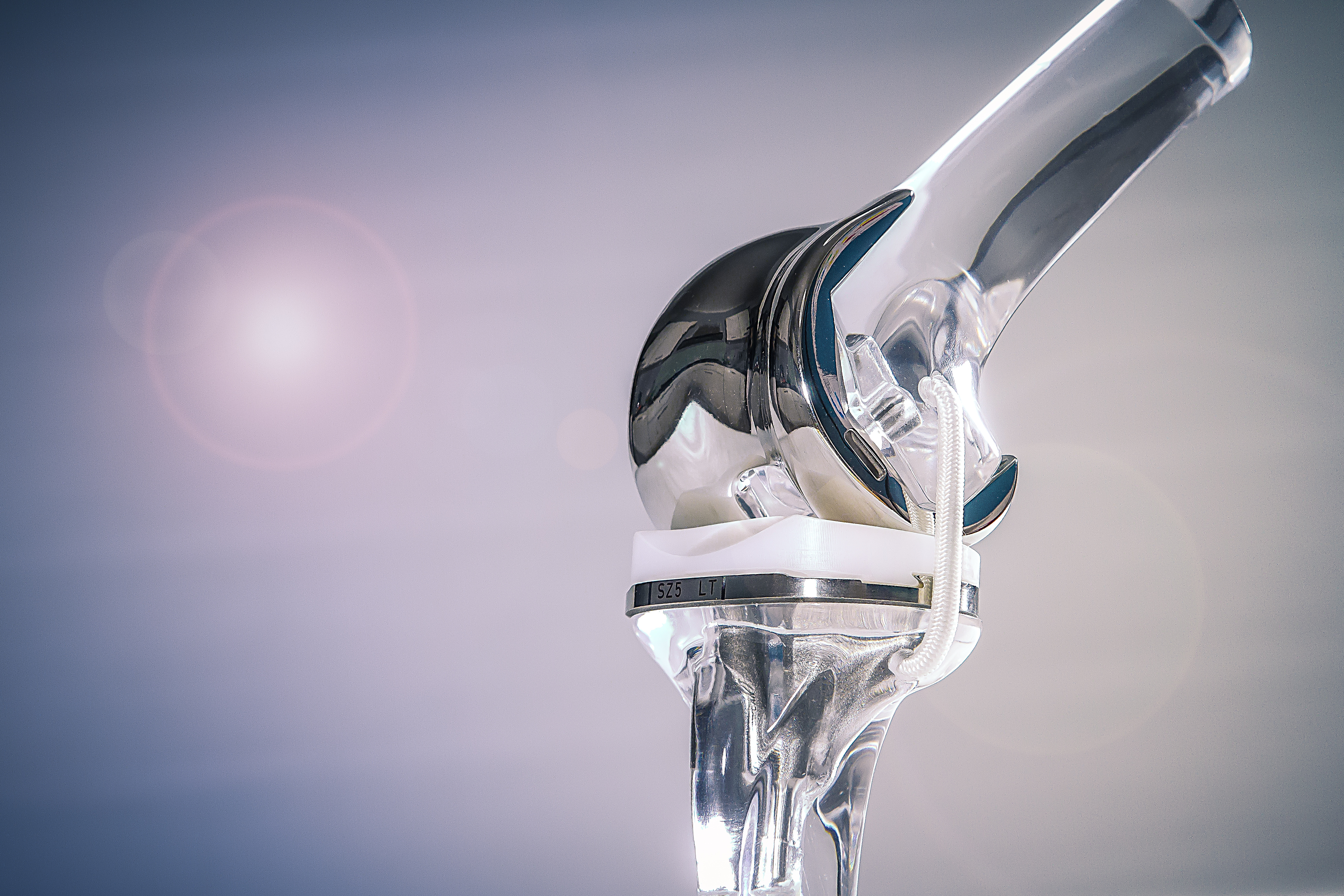
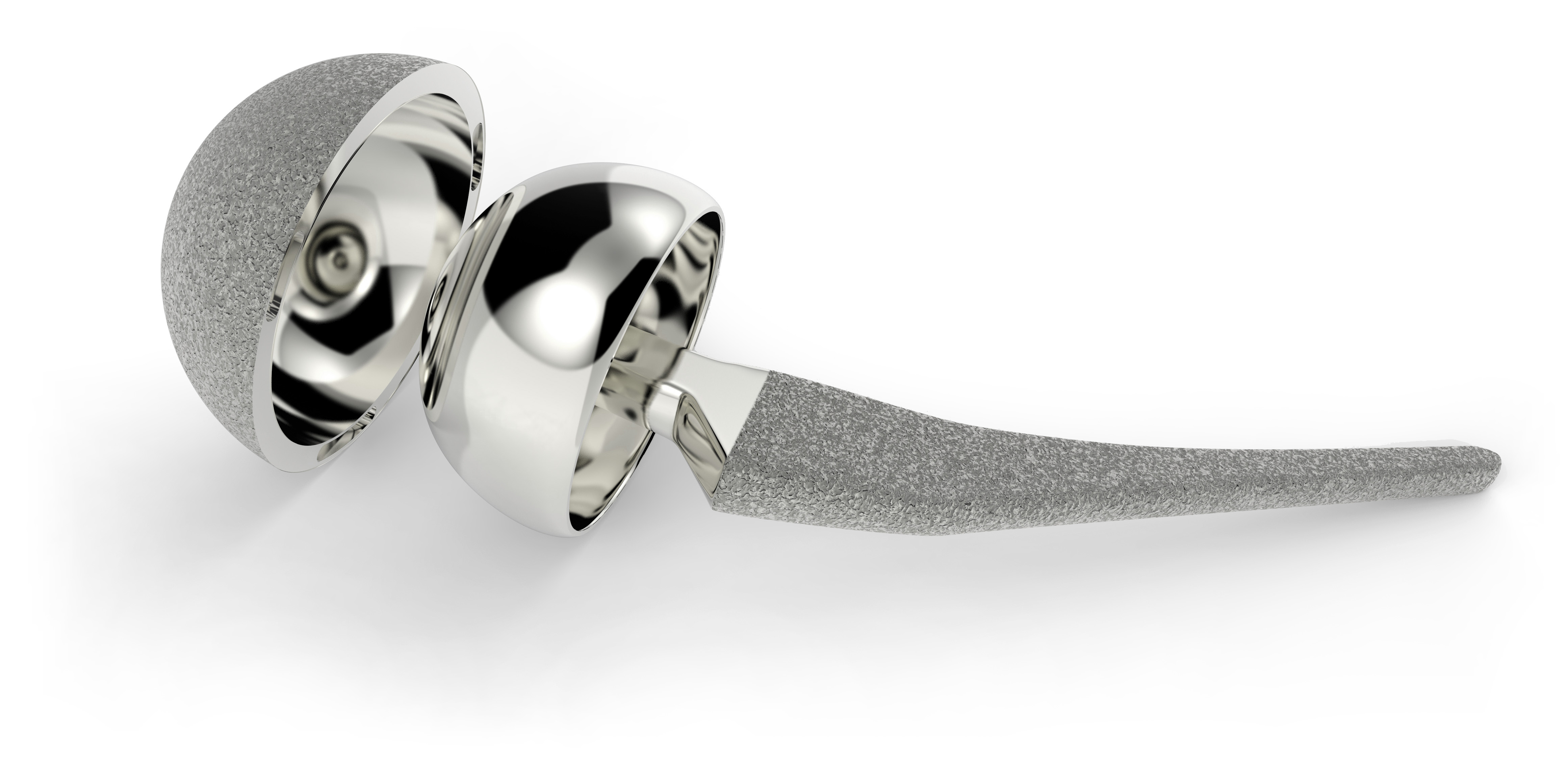

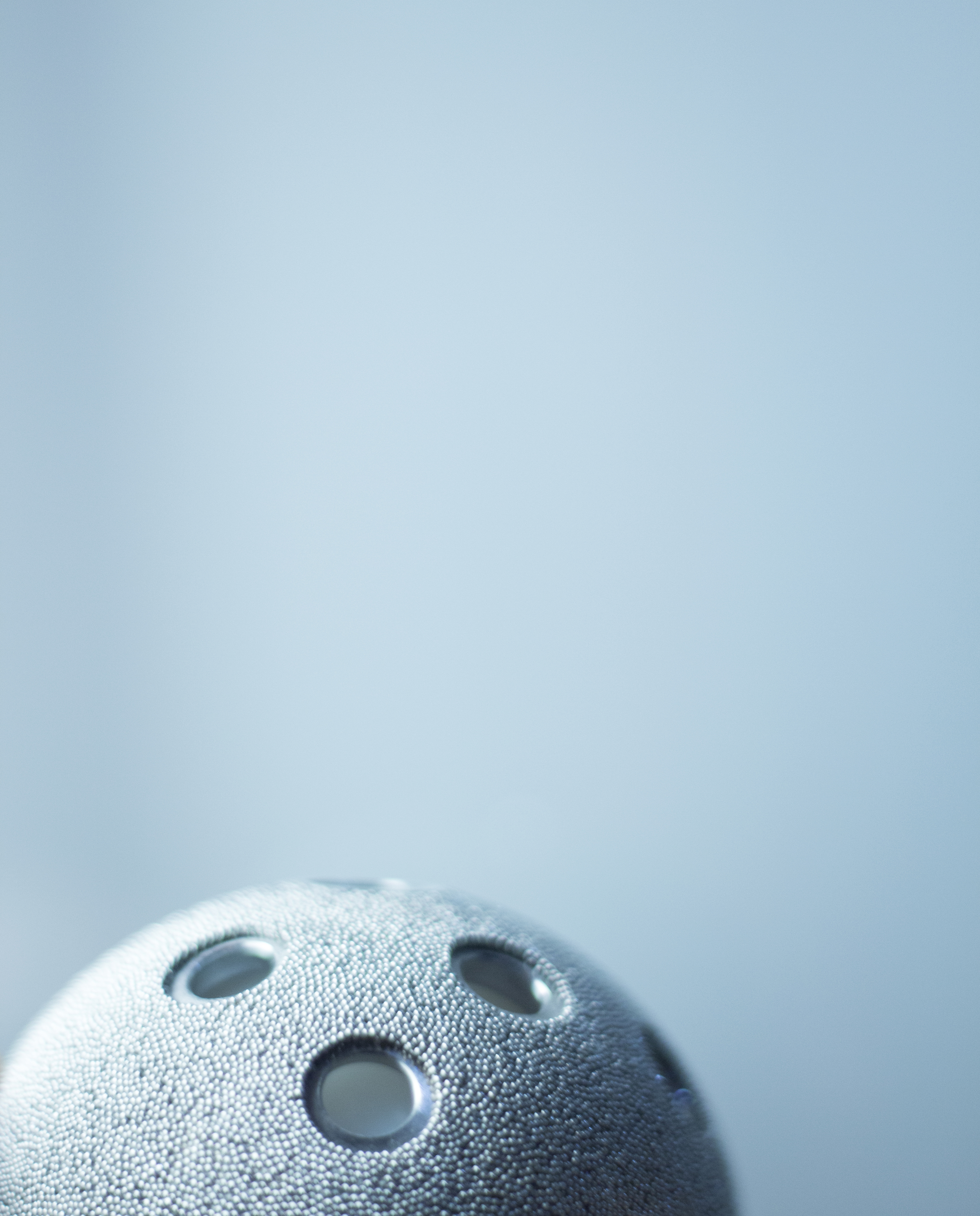
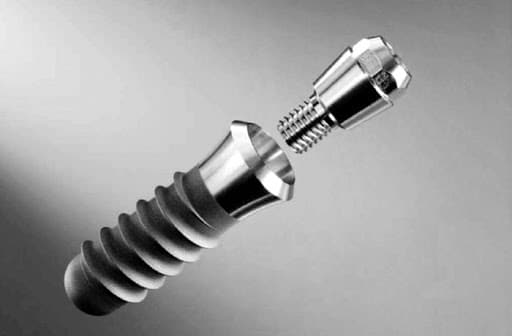
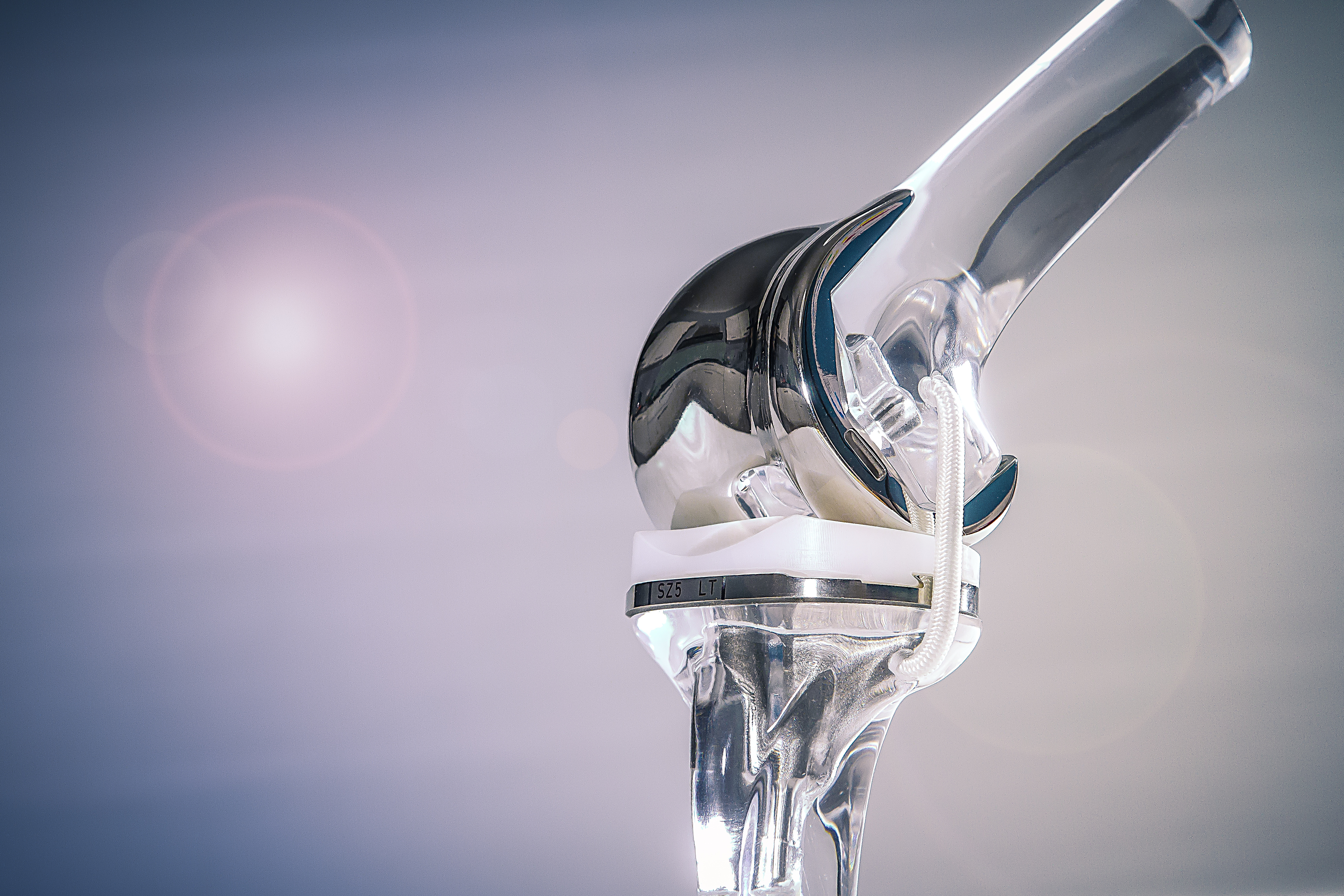
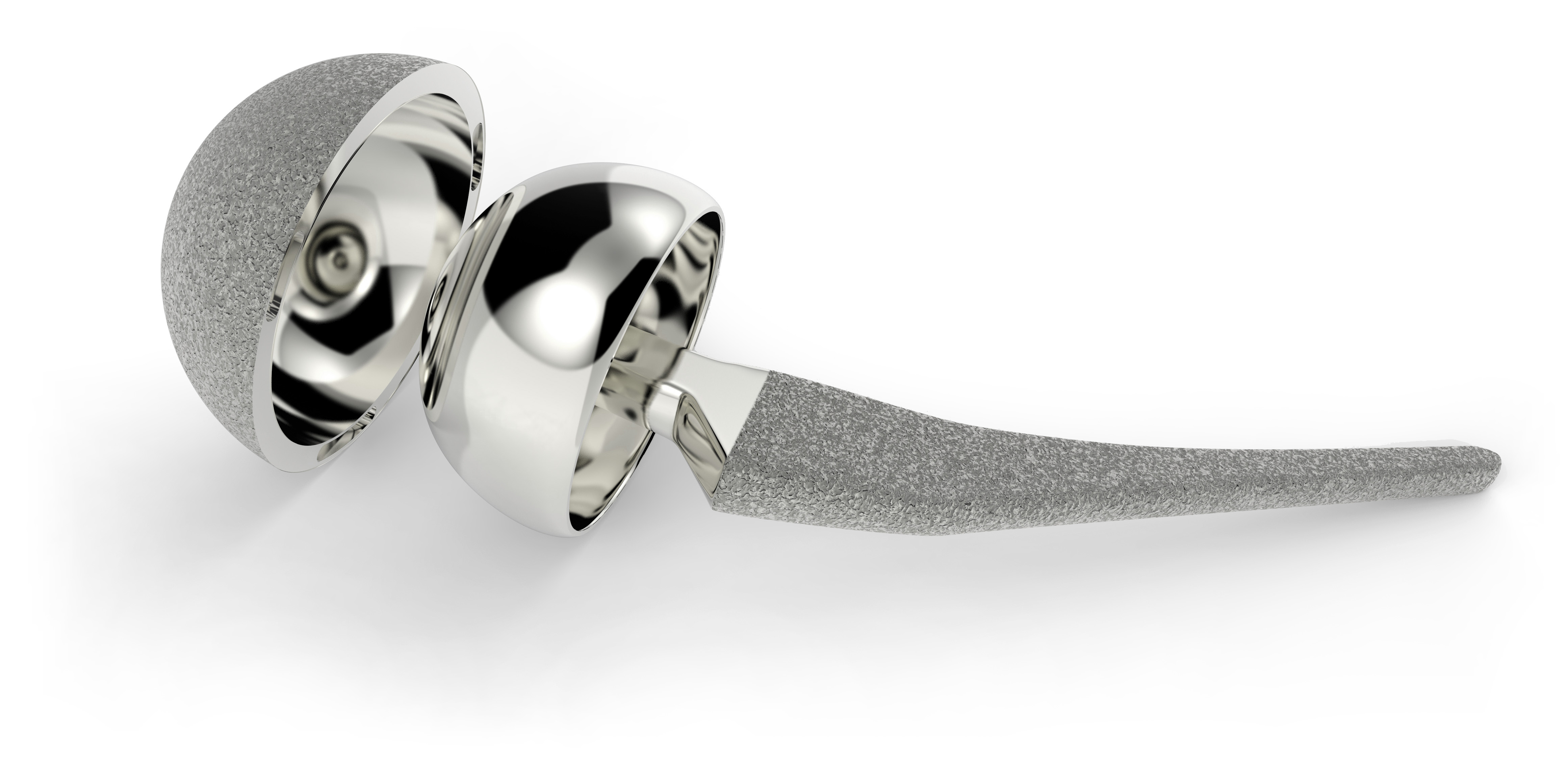

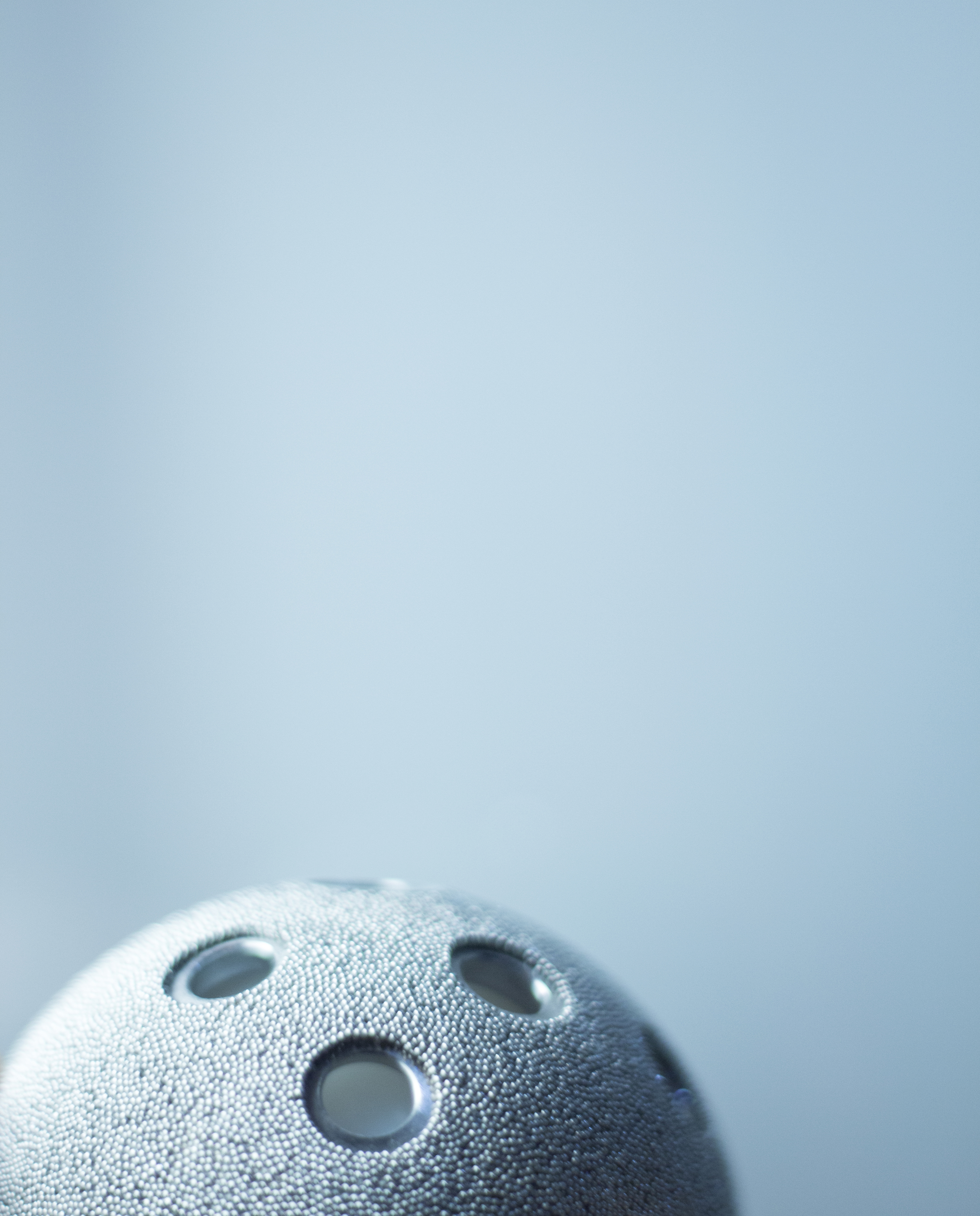
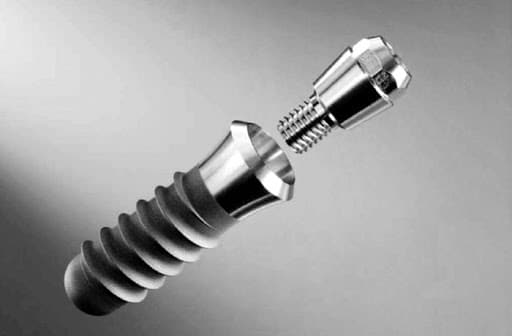
MAIN BENEFITS OF USING HPP
The Hot Isostatic Pressing (HIP) technology developed by Hiperbaric offers the following advantages for the medical implant industry:
Improves material properties and performance
- Increases the fatigue life of the implants.
- Improves the ductility and resilience of materials.
- Allows parts with homogeneous fine grain microstructure, without anisotropy, to be obtained.
Reaches 100% of theoretical density
- Densifies porosities and eliminates internal material defects.
- Homogenizes the properties of the material.
- Allows lighter and/or more lightweight designs.
More efficient production in manufacturing processes
- It reduces the number of parts that would not pass quality control, thus reducing costs.
- Allows the combination of different treatments in a single HIP cycle.
- Hiperbaric's HIP presses make the HIP process an efficient, essential process for the manufacturing of strong and durable medical implants.
Certificates
Several quality standards are applied in this sector. These include the following:
- ISO 13485:2016. Applicable quality management system for medical devices. This standard sets the requirements for manufacturers, installers and service providers of medical devices.
- ISO 10993-1:2018. Biological evaluation of medical products. Part 1: Evaluation and testing through a risk assessment process. Focuses on the evaluation of the biocompatibility of materials used in medical instruments.