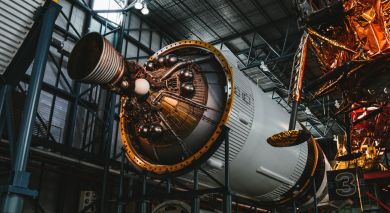
Hiperbaric’s HIP equipment increases the fatigue strength and eliminates porosity of high-performance components manufactured by AM.
Hot Isostatic Pressing (HIP) is a manufacturing process used for densification of both metallic and ceramic components. It is a technology based on the simultaneous application of high pressure (up to 2,000 bar) and high temperature (up to 2,000 °C) through an inert atmosphere (usually argon gas) in order to densify and improve the mechanical properties of critical components for the most demanding sectors such as aerospace, medical-prosthetics, energy and defense.
“HIP is a technology with multiple synergies between the most commonly used industrial manufacturing techniques,” explains Óscar Meabe, Hiperbaric’s Materials Engineering expert. The elimination of shrinkage in casting or injection molding processes, the manufacture of Near Net Shape components in powder metallurgy, the joining of materials with dissimilar properties by Diffusion Bonding or the densification of parts manufactured by additive manufacturing are some of its applications. “It can be said that it is an enabling technology, which makes it possible to make the leap from components with standard properties and uses to applications that require the highest performance,” he explains.
HIP improves components manufactured by AM
Additive manufacturing is a technology that, thanks to its flexibility, compatibility with a wide range of materials and geometric freedom in design, has positioned itself as a key manufacturing process in the most advanced industries. However, it presents a series of intrinsic defects in the process, such as porosity, lack of fusion, anisotropy, etc.
“Thanks to HIP technology it is possible to densify and eliminate internal porosity, increasing the fatigue strength and mechanical properties of the material. On the other hand, the directionality of the material (anisotropy) is eliminated, providing a more isotropic and homogeneous material, reducing dispersion in manufacturing and obtaining a more predictable material,” says Meabe.
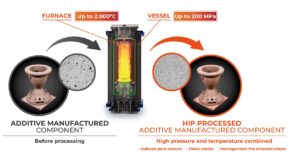
Operation of Hiperbaric HIP technology
Since its origin in the 1950s for the manufacture of nuclear fuel element assemblies by diffusion bonding, HIP technology has been evolving, adapting to the needs of new materials and their requirements.
Hiperbaric’s innovation and experience in high pressure processing has enabled the manufacture of modern HIP equipment, improving performance and reducing costs. Its coiled vessel technology not only has advantages from a safety and reliability point of view, such as increased service life or the “leak before break” design that avoids catastrophic failures, but also provides advantages from a thermodynamic point of view. Being a coiled vessel, the cooling channels can be placed very close to the vessel wall and therefore very close to the hot zone, allowing the vessel to act as a heat exchanger, enabling fast cooling (Fast Cooling technology) inside the equipment.
Through a fan and valves located in the lower part of the oven, forced convection is activated by circulating the hot gas through a heat exchanger located in the upper cap, which exits and descends in contact with the wall of the vessel (which is cooled) and re-enters the oven.
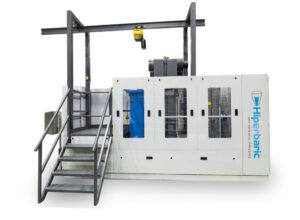
“The ability to rapidly cool within the HIP equipment, in addition to the obvious advantages in terms of increased productivity, reduced production times and energy consumption, which translates into savings, has a number of advantages from the point of view of the material, improving the microstructure and physical properties,” says Óscar Meabe. Thanks to rapid cooling, it is also possible to carry out heat treatments within the same equipment, opening the door to combined cycles (Combined HIP – Heat Treatment, CHIP-HT).
The possibility of carrying out combined heat treatments is very attractive for processing special materials such as nickel-based superalloys, “of great interest to the aerospace sector, or precipitation-hardened steels, where the properties achieved after heat treatment are of great relevance to the defense sector,” he explains.
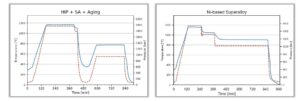
HIP, state-of-the-art technology for the aerospace industry
Thanks to Hiperbaric’s fast cooling HIP technology, it was possible to perform a HIP cycle on a part fabricated by Additive Manufacturing on a copper alloy developed by NASA, GRCop-42. “This copper-chromium-zirconium alloy with high conductivity and strength, reinforced by dispersion, is used in high heat flux applications, such as liquid propulsion rocket engine combustion devices,” he explains.
The component, printed using AM by Aenium Engineering S.L., and owned by Pangea Aerospace, is an aerospike engine that was successfully tested for ignition. This component was processed at Hiperbaric’s HIP Innovation Center in the city of Burgos, where the company has HIP equipment for testing with expert advice. This is the only test center with HIP technology located in southern Europe.
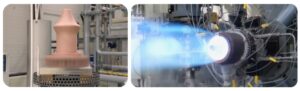
At Hiperbaric, world leaders in the manufacture of high pressure technology applied to various sectors, we have extensive R&D know-how developed over the last 25 years. Based in Burgos, we design and develop Hot Isostatic Pressing (HIP) technology and have the most reliable range of equipment on the market.
To learn more you can contact us here.