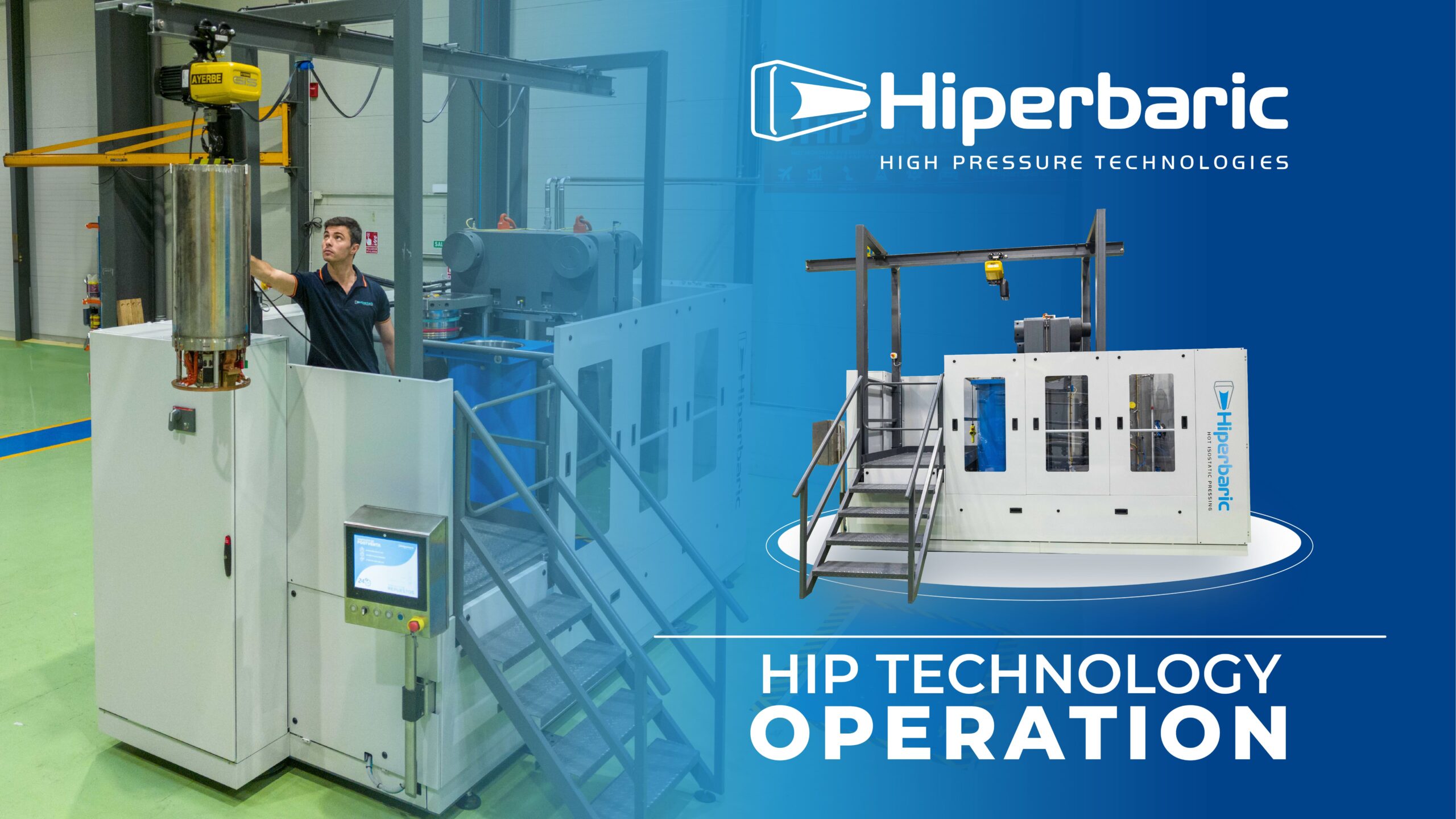
Hiperbaric, world leader in High Pressure Technologies, has become an international reference in the development of industrial Hot Isostatic Pressing (HIP) equipment. Let’s learn more about how the technology works and what are its main features and advantages.
What is Hot Isostatic Pressing (HIP)?
HIP (Hot Isostatic Pressing) technology is a revolutionary heat treatment that applies high levels of pressure, up to 2,000 bar, and temperature, up to 2,000 degrees, through an inert atmosphere to high-performance metallic or ceramic components. The objective is to densify and remove internal defects in metallic or ceramic materials to improve their properties, especially fatigue resistance.
How does Hiperbaric’s Hot Isostatic Pressing technology work?
HIP technology works in the same way in all Hiperbaric presses. In this complete video we explain step by step this process in our equipment.
Operation of a Hiperbaric HIP Press:
- The metal or ceramic components are loaded into the furnace, which is transported with the help of a crane or hoist into the press. The press is closed and locked with the top plug and yoke.
- The vessel is then filled with argon gas, which is stored in standard 200 or 300 bar cylinders, which also feed the compressor used to raise the pressure to 2070 bar.
The compressor, manufactured by Hiperbaric, is based on a two-stage technology whereby the gas is compressed in the first chamber to an intermediate pressure. As it leaves the first chamber, it is cooled and finally enters the second chamber where it is compressed. The chambers of both stages have an innovative design to cool them more efficiently, giving the high-pressure seals a longer service life.
- The user can define the pressure and temperature rise parameters according to the requirements of each process, being possible to define complex cycles with several heating and cooling stages.
- At the end of the pressure and temperature maintenance stage, it is possible to use the Fast Cooling technology, an exclusive Hiperbaric development. This technology extracts heat from the batch of heat-treated components quickly and uniformly and allows heat treatments to be performed during the HIP cycle.
- During the temperature rise and hold stages, hot gas flows between the parts and the heating elements with the help of a fan to improve temperature uniformity.
- When the ‘Fast Cooling’ technology is activated, a series of valves allow the hot gas to flow to the heat exchanger located in the top cap. Additive manufacturing has made it possible to design an efficient and compact exchanger that extracts a large amount of heat from the gas before it hits the vessel.
- Once cooled, the gas re-enters the hot zone where it mixes with hot gas before impinging on the parts, thus achieving uniform cooling.
- At the end of the process, the argon is removed from the vessel and the furnace can be removed from the press.
For more information, do not hesitate to contact us, you can download our flyer here, or contact here an expert who will inform you about everything.