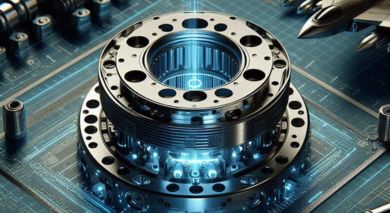
This study analyzes Hot Isostatic Pressing (HIP) benefits in a Ti-6Al-4V alloy fabricated using Binder Jetting. The conventional HIP cycle and high-pressure lower-temperature HIP cycle (HIP-HPLT) are compared. The results show how HIP-HPLT process produced a significant increase in properties compared with as-sintered parts and conventional HIP. Furthermore, impurities content such us oxygen play a critical role in the final mechanical properties.
Binder Jetting (BJ) is an additive manufacturing technology in which a liquid bonding agent is selectively deposited onto powder to create a 3D “green” body, which is then densified through a high temperature sintering. Thanks to its versatility and flexibility offers several advantages including:
- Compatibility with a wide range of materials
- Room temperature process. Avoiding residual stresses and microstructural changes.
- High production rate and large part volumes.
However, it has several drawbacks compared with other AM processes, mainly due to the high porosity and coarse microstructure that results from the sintering process. As-printed parts typically have a low relative density of about 60%, which increases up to 95% after the sintering stage. The properties at this point are acceptable, although insufficient for very demanding applications such us aerospace, defense, medical implants, energy, etc. where materials need to meet the highest requirements.
For this study, Ti-6Al-4V (Ti64) has been chosen since it is a very interesting material and one of the most used in these areas, thanks to its low density, stiffness and toughness. Nevertheless, the Ti64 shows an additional drawback when manufacturing via BJ. The ink used for BJ is typically a water-soluble polymer (binder), after printing a de-binding process is carried out before sintering to remove almost completely this water-based agglomerant. However, any residual binder constituents will be decomposed into their elemental constituent during the sintering cycle. Carbon (C) and Nitrogen (N) are impurities that can reduce the mechanical properties of the component, being the Oxygen (O) the most critical impurity. An increase in oxygen content leads to a higher tensile strength but significantly reduces the material ductility and affects the fatigue life of the resulting component.
Since the remaining porosity after sintering is around 5%, to “upgrade” the BJ applications post-treatments are required. Hot Isostatic Pressing (HIP) is one of the best processes to improve the performance of AM parts. In this process a component is subjected a combination of high pressure and high temperature for a holding time in an inert-gas-pressurized environment to remove internal porosity and densify the material leading to an increase in fatigue resistance and microstructure changes in Ti alloys.
In this study two HIP cycles are explored in BJ-Ti64:
- Conventional HIP cycle: Temperature range of 900-920 °C, under 100-120 MPa for a holding time between 2-4 h in an argon atmosphere followed by furnace cooling.
- Higher Pressure, Lower Temperature HIP (HIP-HPLT): Temperature range between 820-850 °C under 200 MPa for 2 h in an argon atmosphere and rapid cooling
Microstructure
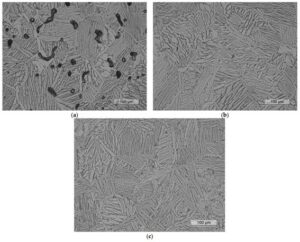
From a microstructural point of view after either HIP process, nearly all the internal voids were eliminated. However, some isolated voids near the surface were not removed due to the prior elongated voids that were connected to the external surface of the part. This is because the pore, being connected to the surface, can’t close since the argon enters inside.
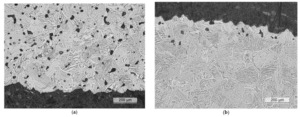
Tensile test
The tensile properties obtained after both HIP treatments demonstrated an appropriate strength value that was comparable with that of the PBF + HIP process, but the deformation capacity was lower. Furthermore, a slight improvement in the performance was observed in the low-temperature high-pressure HIP cycle.
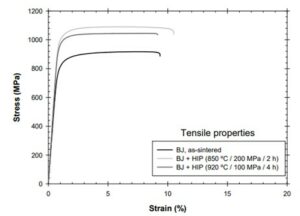

Fatigue
The fatigue resistance exhibited by the BJ-Ti64 was poor, although an improvement was observed after the HIP treatment, its fatigue limit was much lower than that of the material manufactured by PBF. These unfavorable fatigue properties of BJ material could be attributed to the high internal porosity after sintering, the thickness of the α laths, and the oxygen content that promoted the formation of oxygen-enriched particles, increasing the local stress concentrations, and thus, reducing the fatigue performance.
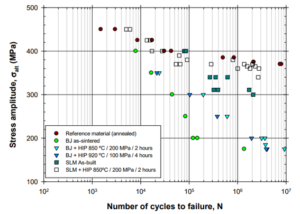
Conclusions
- The tensile and fatigue performance of the as-built condition was significantly poor, due to the high residual porosity after sintering and residual oxygen from binder.
- After the HIP treatment, the tensile strength improved to levels comparable with Ti64 produced by PBF. However, the deformation capacity remained limited due to the oxygen content.
- The fatigue life also improved compared with the as-built condition, although still lower than those observed in PBF subjected to the same HIP treatment.
We can conclude that to utilize Ti-6Al-4V manufactured by Binder Jetting in components intended for high-load conditions, HIP post-treatment is essential to densify the material and improve the properties, but additionally, binder jetting processes or alternative binders need to be developed in order to limit the oxygen content after de-binding. You can find the full scientific article here.